
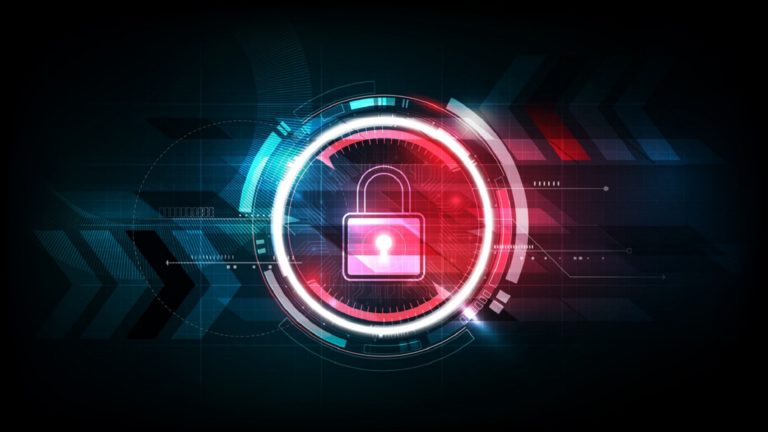
- #WATCH LINKEDIN LEARNING SOLIDWORKS XDESIGN FULL#
- #WATCH LINKEDIN LEARNING SOLIDWORKS XDESIGN SERIES#
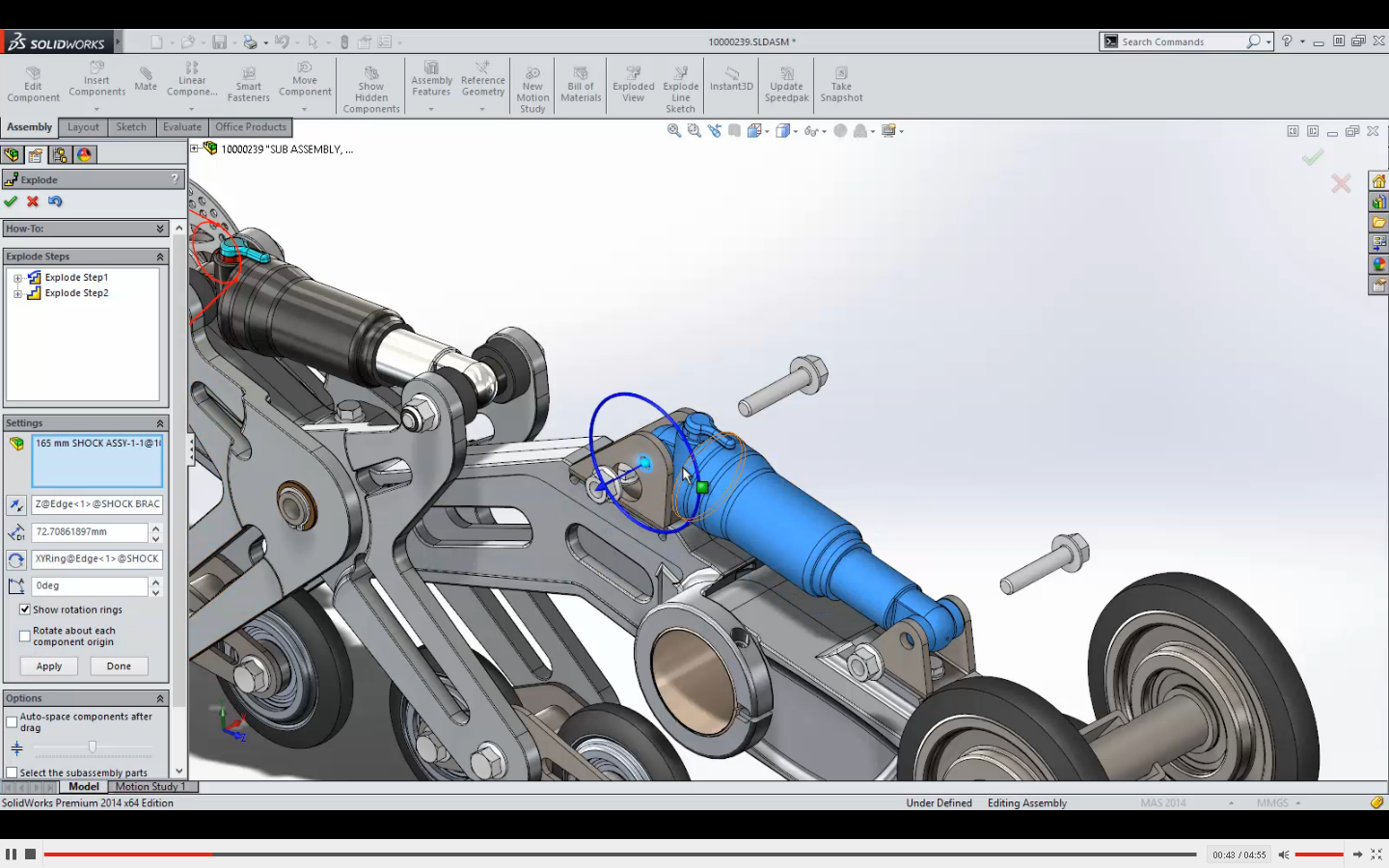
Not only can an Extrude feature be changed to an Extrude Cut, it can even be transformed into a Revolve or ,in this case, a Sweep. Relationships can be applied to both ends of the spline, and the handles can be adjusted until it looks just right.ĭon rolls the model forward to edit the original Extrude feature.
#WATCH LINKEDIN LEARNING SOLIDWORKS XDESIGN FULL#
Starting with a two-point spline, he can activate the spline handles to achieve full control over the curvature. To accomplish this, he can roll the design back before the Extrude feature to create a curved path. While extruding the feature, a preview is displayed making it easy to confirm the correct end condition has been applied.īut on second thoughts, Don is underwhelmed with the resulting shape, and would prefer a sleeker look. These relations will fully define the sketch. Sketched ellipses include construction lines making them easy to orient.įor example, Don can snap the quadrants of the ellipse to the midpoints of external model edges, or he can also click on both the point and the edge, opting to create the same relationship in the pop-up menu. By preselecting a face in context of the assembly, he can skip the sketch and extrude his first feature. To start, Don can create a mounting flange with little effort.
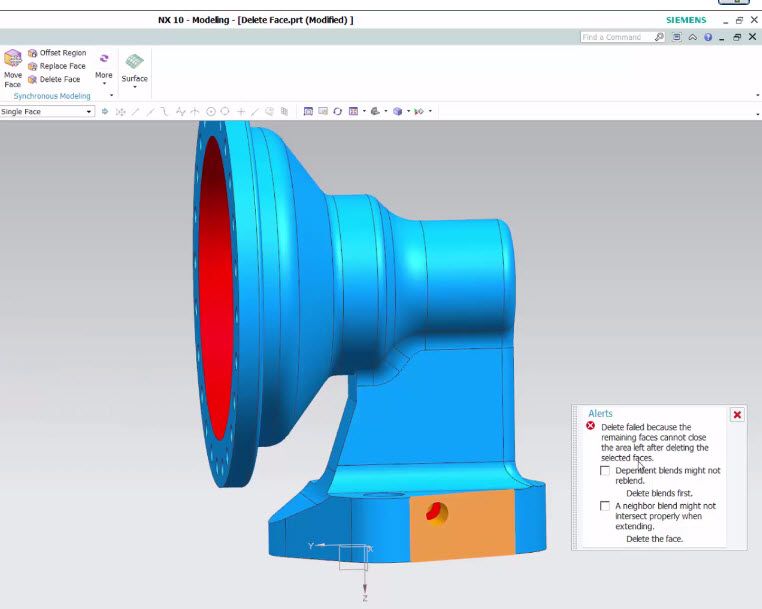
With the ability to create sub-divisional models directly in a browser on any device, complex shapes have never been easier to create.ģDEXPERIENCE® Works cloud-based design apps for Mechanical DesignĪfter starting the design in 3D Sculptor to create the ergonomic grip handle, it’s now been turned over to Don, the Mechanical Engineer, to complete the design and prepare it for manufacturing with 3D Creator.ĭon will need to create the stem connecting the body of the circular saw to the grip handle. This streamlines the communication process allowing teams to arrive at the perfect design faster than ever.

This allows Dan to check his edits from multiple angles without having to continually wrestle with zooming and panning.įinally, to collect feedback from the rest of his team, Dan can post the entire 3D model to a community directly from the design app. As views change, the area of focus stays cantered on the screen. And by double-clicking the copied Subdivision feature, Dan can get started on his first concept of the grip while leaving the original start shape intact.īy utilising the Alt+Drag scaling technique, Dan can wrap up this concept in no time. Each feature set can have unique colour properties and display states. He can simply copy and paste features from one set into another. In this case, Dan would like to propose various concepts of this grip, by creating a new feature set for each of his concepts. Opening the door to many creative workflows, multiple sets of features can be created within a single Physical Product. This shortcut will generally scale in all three dimensions, but since this face was planar, it conveniently maintains its flatness. To maintain a uniform aspect ratio while scaling this side face, Dan can hold the Alt key while dragging any of the scaling dots on the robot manipulator. This makes translating an entire shape to a new position a breeze. Using the Ctrl+A keyboard shortcut, all vertices are selected at once.
#WATCH LINKEDIN LEARNING SOLIDWORKS XDESIGN SERIES#
‘Scale by Distance’ applies a parametrically-driven ‘Bounding Box’ where he enters a series of dimensions, and the shape snaps precisely to size. With 3D Sculptor, Dan can freely push and pull the model into any shape imaginable, but, most of the time designs are required to fit within a specific boundary. Since flat faces will be incorporated into this design, he can get a head start by checking the ‘Crease Edges’ option while placing his initial shape. Getting started is easy, Dan picks a cylinder and drops it directly on the origin. Let’s drop in on Dan as he shapes a grip handle with 3D Sculptor. Dan’s a mechanical engineer who will prepare the models for manufacturing. 3DEXPERIENCE® Works cloud-based design apps for Industrial Designĭan’s our industrial designer in charge of ergonomics and aesthetics. In this demonstration, you’ll see an entire design process on multiple components of a circular saw from concept to manufacturing, entirely within a web browser. With the 3DEXPERIENCE® Works Platform, you can design on the cloud using any device without sacrificing the performance and power you need to stay productive no matter where you are. But with more people working remotely than ever before, you need a more flexible environment. As a designer, you’ve always required the most powerful (which usually means the most expensive) workstations.
